Fuel tank flammability mitigation is a critical aspect of ensuring aviation safety. To that end the Federal Aviation Agency (FAA) issued its Fuel Tank Flammability Reduction (FTFR) rule in 2008. Twelve years later, the FAA launched another round of directives related to the Fuel Quantity Indicating System (FQIS). Both rules outline options for safeguarding against fuel tank ignition, the primary of which are nitrogen inerting systems and fuel tank ignition mitigation means (IMM).
A wide variety of factors can contribute to fuel tank ignition, from electrical ignition and lightning strikes to electrostatic discharges, and in military applications, even gunfire. Fuel tank explosions have affected 18 aircraft since the 1950s, and most recently, caused the third deadliest accident in U.S. aviation history: TWA Flight 800 in 1996. Given these statistics and the dynamic nature of fuel tank chemistry, the need for the FAA’s flammability reduction mandate is clear. What’s less clear to many in the commercial aviation industry is the best process for ensuring fleets are fit to fly per the requirements of the FTFR and the FQIS rules—especially navigating the two types of solutions and exemptions acceptable as stated in the FAA mandates.
Here’s your quick primer on the difference between nitrogen inerting systems and fuel tank ignition mitigation solutions, along with a few best practices to help you choose the best option to get your fleet in compliance with the FQIS and FTFR rules.
How Do Nitrogen Inerting Systems Work in Aircraft? 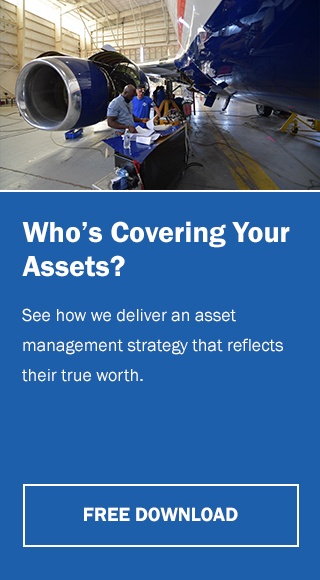
At their most basic level, nitrogen inerting systems maintain a certain amount of nitrogen, or another nonreactive gas, in an aircraft’s fuel tank in order to decrease the risk of combustion. As an aircraft consumes fuel during flight, oxygen is replaced with nitrogen to keep its ullage—the volume in the fuel tank above the fuel, where fuel vapor is found—at a ratio that reduces the risk of ignition.
A key feature of nitrogen inerting systems is the air separation module (ASM). As its name implies, the ASM separates air using a permeable membrane that allows oxygen to flow out and nitrogen to flow in. Because ASM fibers are damaged by high levels of ozone, these separators require regular, robust maintenance, and eventually replacement. The ASM component is critical to the system’s overall functionality and requires that the aircraft be running and the bleed air system supplying bleed air to the ASM for the Nitrogen Generating system to work, resulting in additional fuel burn.
When evaluating nitrogen inerting systems, ensure you have a robust MRO strategy to avoid an AOG and a clear understanding of the downtime needed for installation. Because these systems require structural changes to an aircraft, additional time on the ground should also be factored into your cost evaluation. Lead time for these systems is typically one year.
The Benefits of Fuel Tank Ignition Mitigation Means (IMM)
Like nitrogen inerting systems, fuel tank ignition mitigation solutions limit the amount of oxygen available in the fuel tank. However, the similarities stop there—and the distinctions are key to understanding the best solution for your fleet’s FTFR and FQIS rule compliance.
AerSafe®, the fuel tank ignition mitigation solution created by the aerospace engineers at AerSale®, uses custom-designed, precision cut reticulated polyurethane foam blocks to line the cavity of an aircraft’s center fuel tank. FAA approved and designed to meet the exact tolerances required to fill the fuel tank cavity of specific Airbus and Boeing series aircraft, this foam block system mitigates the effects of fuel vapor ignition, ensuring that an explosion does not occur. The full tank foam inserts provide immediate and reliable protection, offering a cost-effective solution with minimal maintenance requirements and no costly parts (air separator module - ASM).
Because fuel tank ignition mitigation solutions like AerSafe don’t require structural changes to an aircraft, installation is more streamlined and has been optimized for easy installation. With narrow-body aircraft, for example, AerSafe installation takes roughly two days: for wide-bodies, five days. AerSafe is equipped with a prefabricated kit that makes it possible to install our solution at any hangar around the globe, with a lead time of just four (4) to six (6) weeks.
The AerSafe system also brings another major benefit when compared to a nitrogen inerting system: there are no hard-time or life-limited components to replace, additionally, there is no requirement for post-installation flight tests. The AerSafe system is fully functional, and the center fuel tank is protected once the system is installed. There is no need to have the aircraft running, nor is there a requirement for bleed air or an electrical interface. Making AerSafe an efficient and cost-effective choice for your flight operation.
AerSafe is FAA approved as a fuel tank ignition mitigation means (IMM) solution under 14 CFR 25.981 (a) (c) (d). The system is available for the following aircraft:
- Airbus 319 and 320 (FAA STC No. ST04010NY)
- Airbus 321 (FAA STC No. ST04010NY and EASA STC No. 10065226)
- Airbus 330 (STC Pending Approval)
- Boeing 777 Series (FAA STC No. ST04203NY)
- Boeing 767 Series (FAA STC No. ST03599NY)
- Boeing 737 NG Series (FAA STC No. ST02980NY)
- Boeing 737 Classic Series (FAA STC No. ST03589NY)
Beyond FAA approval, the AerSafe system is approved by multiple aviation authorities around the world.
Are you ready to ensure your fleet is FQIS and FTFR rule compliant with less downtime and lower costs? Let’s talk about how AerSafe delivers more value than a nitrogen inerting system.